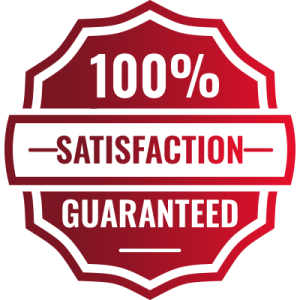
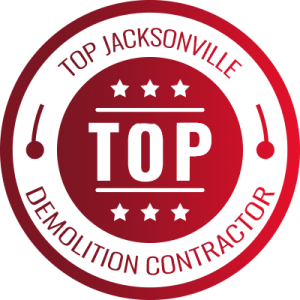
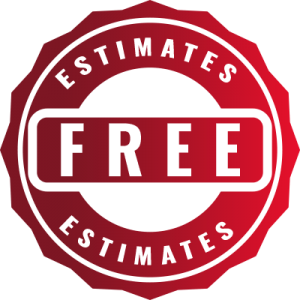
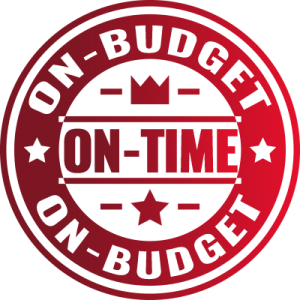
Hazardous materials can pose a big risk during commercial demolition. They’re not always visible, and when disturbed, they can create safety and environmental problems that delay the project or add unexpected costs. Before any walls come down or equipment moves in, it’s important to figure out what’s in the building and deal with it the right way. That’s not just good planning, it’s required if you want things to go as smoothly as possible.
In Jacksonville, older commercial buildings often hide materials like asbestos, lead-based paint, and other hazardous substances that were once common in construction. These materials don’t go away over time. If disturbed, they can enter the air and harm workers or cause problems for nearby properties. So before beginning demolition, taking steps to locate and safely remove hazards is a must. It protects workers, keeps the job on track, and avoids trouble with building inspectors or environmental agencies.
Identifying Common Hazardous Materials
Safety starts with knowing what might be inside the building. Certain hazardous materials were widely used in commercial structures, especially those built before stricter regulations kicked in. Locating these materials early in the process plays a big role in keeping the demolition safe and compliant.
Here are some of the most common hazards found in Jacksonville-area commercial buildings:
– Asbestos: Frequently found in insulation, ceiling tiles, pipe coverings, floor tiles, and roofing materials. Asbestos was widely used because it resisted heat and fire. The problem is that when it’s broken or disturbed, it releases fibers into the air that, if inhaled, can cause serious health problems.
– Lead Paint: This shows up most often in older buildings on walls, doors, windows, and metal railings. While it’s not harmful unless disrupted, scraping or sanding can release lead dust that’s harmful to workers and anyone nearby.
– Mold: Florida’s humid weather makes mold one of the more common problems in properties that have had roof leaks or poor ventilation. Mold spreads fast and can cause health issues, especially through the HVAC system during demolition work.
– Other Hazardous Materials: Older electrical systems might contain PCBs (polychlorinated biphenyls), which were used in transformers and fluorescent light ballasts. Mercury is another concern found in old thermostats, switches, and some light bulbs.
For example, a small office building in Jacksonville faced delays after discovering old mercury-containing thermostats during a pre-demolition walkthrough. Because mercury requires special handling and disposal, it ended up adding both time and cost to their otherwise straightforward demolition.
Every building is different, but understanding these risks up front makes it much easier to build a demolition plan that keeps workers safe and the job compliant.
Pre-Demolition Inspection
Before any demolition can move forward, a thorough inspection is the first step. This helps identify exactly where the hazardous materials are and what type of removal plan needs to be in place. In Jacksonville, this process is especially important due to the high number of older commercial properties that may still contain these materials.
Here’s how a proper inspection should go:
1. Hire Certified Environmental Inspectors: This isn’t a job for guesswork. Professionals who are trained and licensed will know where to look and how to take samples without spreading contamination.
2. Walk Through the Property: From crawl spaces to attics, materials need to be visually inspected and tested if there’s any doubt. Inspectors usually take samples of suspected asbestos or lead and send them to a lab for confirmation.
3. Review Building Records: If the building has blueprints, renovation history, or construction records, those can reveal key info about what materials were used and when.
4. Document Everything: The findings from this inspection should be written up in a formal report. This documentation is usually required to get permits for commercial demolition in Jacksonville and can also help with planning the safe removal of materials.
5. Notify Building Officials: If hazardous materials are found, the information may need to be shared with local authorities before removal begins.
Once the inspection confirms the presence of hazardous materials, the next step is safely removing them. Without that inspection, there’s a big risk of exposure, delay, or heavy fines. A solid plan always starts with good information.
Safe Removal Procedures
Once the inspection is done and hazardous materials are identified, the next move is safe and professional removal. This step has to be carefully mapped out. In a commercial demolition project in Jacksonville, skipping over one detail could mean delays, safety violations, or exposure problems. The removal process should match the findings from the inspection and follow approved safety rules every step of the way.
Start with a removal plan. That includes when the materials will be taken out, what equipment will be used, and who will be assigned to each task. This plan also sets up timelines and lets everyone know what areas will be off-limits during the work.
Containment is another key part. Hazardous materials have the potential to contaminate more than just the demo site. To keep everything contained, use proper sealing, negative air systems, and specialized barriers. For example, sealed plastic sheeting can create a contained work zone while air filtration units scrub the air as workers remove contaminated material.
Each type of material has different removal needs:
– Asbestos needs to be kept wet during removal to stop airborne fibers from spreading. Licensed teams wear full protective gear and use sealed disposal bags.
– Lead-paint cleanup might involve chemical stripping, hand-sanding with HEPA vacuums, or complete removal and replacement of painted sections.
– Mold removal starts after moisture issues are handled. Affected materials like drywall, carpet, or insulation are removed under containment. Damaged areas are dried out and cleaned with mold-killing agents.
– PCBs, mercury, and other chemicals often need hand removal of parts like ballasts or thermostats, followed by proper packaging and labeling for disposal.
Disposal isn’t just loading up a truck and heading to the landfill. These materials often need to be transported to licensed facilities that handle specific types of hazardous waste. Making sure they’re sealed, labeled, and tracked helps avoid fines and potential leaks during transit.
Compliance With Local And Federal Regulations
In Jacksonville, demolition rules around hazardous materials aren’t the kind you can afford to ignore. Federal agencies like the EPA set standards, but so do Florida’s environmental offices and local city departments. Knowing which laws apply to commercial demolitions in your area keeps the job from getting tangled up in red tape or facing penalties.
Some responsibilities are tied directly to the property owner or contractor. These include:
– Filing notices of asbestos removal for demolition permits
– Following OSHA guidelines during the removal process
– Meeting Florida DEP rules for disposal and cleanup
– Keeping detailed records of materials removed and how they were handled
Hiring certified contractors is part of staying compliant. They’ve taken the proper training and carry credentials showing they’re allowed to remove hazardous materials. These certifications are often required by law when asbestos, lead, or other risks are part of the work.
Record-keeping is more than just checking a box. It helps prove that the job was done right and protects you if a dispute ever pops up. Some common documents include disposal receipts, waste manifests, and air quality test results.
Maintaining Safety During Demolition Work
Hazardous materials aren’t the only risk on a job site, but they do require special care during demolition. Once the removal is done, ongoing steps help make sure that cleanup was thorough and that no surprise exposures occur during the rest of the process.
Start with air monitoring. This helps confirm that asbestos, mold spores, or lead dust haven’t made it into surrounding areas. If readings spike during demolition, teams can stop work and figure out the source before continuing.
Crew training also matters more than people might think. Even if the hazardous materials are gone, workers need to know what to watch for and how to handle a new problem if one arises. That means teaching them to identify things like suspicious wallboard, burned-out light components that may contain mercury, or water damage that could point to hidden mold.
Backup plans are another piece. If cross-contamination happens or protective barriers fail, having emergency procedures ready to go helps limit exposure and get cleanup started fast.
A safe site doesn’t only protect workers. It protects building neighbors, city inspection workers, and future project timelines. Safety checks shouldn’t stop once removal is complete.
Keeping Your Jacksonville Demolition Project On Track
When hazardous materials get handled the right way, the rest of the demolition can move forward with fewer hiccups. You won’t face as many delays for inspections, and the crew won’t have to stop and re-do work because something was missed or done wrong. It also builds trust with nearby property owners, city officials, and anyone else affected by the work.
Taking the time to remove materials like asbestos, lead paint, and mold before demolition sets projects up for success. It keeps workers safe, aligns with building codes, and allows you to move faster once clearance is given. With a complete plan that includes inspection, removal, and disposal, issues can be solved before they turn into bigger problems.
Safeguarding Your Project and Team
Removing hazardous materials is one of the most important steps in any commercial demolition project. It helps avoid exposure, protects workers, and keeps the property in legal compliance. Skipping or rushing through this part of the process can create expensive setbacks and health concerns, sometimes long after the job is done.
For commercial buildings in Jacksonville, following these steps makes demolition safer and more predictable. It provides a strong start and helps projects move forward without unnecessary stops or surprises. Everyone involved ends up with better results when safety, planning, and compliance all work together from day one.
To ensure your demolition project runs smoothly and stays on track, take the necessary steps to remove hazardous materials safely and comply with all local regulations. By focusing on these aspects, you not only protect your team but also streamline the entire process. For expert guidance and support on safe and efficient demolition work, explore our comprehensive commercial demolition services offered here at Elev8 Demolition.